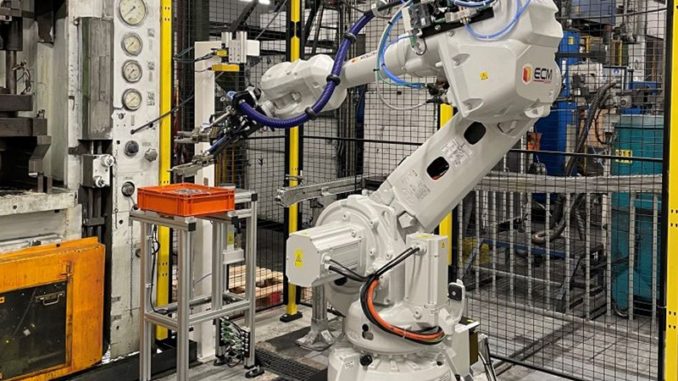
The Next Chapter in Heat Treatment
The challenges discussed in our recent “State of the Gear Industry Survey” follow a similar pattern across the entire manufacturing sector. Skilled labor issues, stricter energy regulations, and a desire to upgrade equipment are just as relevant in heat treating. Today, gear manufacturers would like to replace costly subcontract work for in-house capabilities, and provide additional robotic, automation and green energy benefits to their customers. Low pressure carburizing (LPC) provides a path to these technologies. “Because low pressure carburizing (LPC) is highly repeatable and the recipes just run and run with very little adjustments or tuning, we’re seeing a lot of this technology going in-house at GM, Ford and Stellantis,” said Bill Gornicki, director of sales at ECM USA, Inc. “In addition, thanks to all the new players in the global electric vehicle (EV) market,
we’re seeing new production in China, Europe and India all going to LPC as well,” said Dennis Beauchesne, general manager at ECM USA, Inc. “LPC technology provides a better environment to operate in. It’s more like a machine tool with processing that provides precise and repeatable results, capabilities everyone is looking for in the EV sector.” ECM Technologies developed Infracarb in the 1980s. The Infracarb process is fulfilled under low pressure. The carbon donator gas is Acetylene C2H2 – used during the enrichment phases, and nitrogen N2 is used during the diffusion phases. The process temperature is generally higher than traditional carburizing, between 880 and 1,050°C thanks to the vacuum technology. The high temperature processes help reduce carburizing cycle time in comparison to traditional atmosphere carburizing. Gornicki said the technology opposes everything most people think about when they consider the history of heat treatment. “They’re quiet machines.
There’s no flame, soot or oil. The UAW absolutely endorses this equipment because it’s a pleasure to work with,” Gornicki said. Beauchesne added that ECM has introduced a line of eco-friendly furnaces that will take the place of standard batch IQ furnaces. The organization has won two awards (one from Europe and the other from China) to reduce the carbon footprint. “LPC, in itself, is about a 95 percent reduction in gases being used,” Beauchesne said. “We’re using around 5 to 10 percent of the gases you’d find in an atmospheric furnace. Our goal is to provide eco-friendly equipment that fits with standard equipment so customers can upgrade their heat treat departments more cost effectively over a longer period of time, rather than replacing everything they have at once. This also allows our customers to do other processes that vacuum furnaces provide benefits to such as hardening, brazing, etc.” These green initiatives benefit everyone involved in the supply chain, according to Gornicki. “Automotive companies are judged not only by their own carbon footprint but also the carbon footprint of their vendors. If they’re using commercial heat treat and atmospheric furnaces that all counts toward their carbon footprint. The incremental ability to shift from an existing atmosphere furnace to a vacuum line over time or have both processes on the same line can be advantageous,” he said.